Steel is one of the most important alloys in knife making and one of the most important elements in knife quality due to its high durability and toughness. However, heat treatment allows the steel to be hardened further, improving the performance and quality of the tool. This article will briefly discuss how the steel of a knife is heat treated and how this adds value to the knife and multitools.
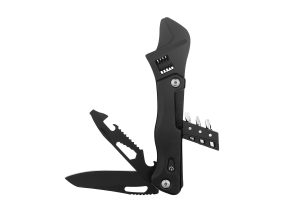
What Is Knife Heat Treatment?
Heat treating knives is a crucial step in the knife-making process, as it allows for the manipulation of the steel’s properties to create a blade that is both durable and efficient. This sequence of thermal procedures involves subjecting the steel to extreme temperatures, followed by controlled cooling, in order to achieve the desired balance of hardness, toughness, and other essential attributes.
The Purpose of Heat Treating Knife Steel
Improved wear resistance: Hardened steel is more resistant to wear and abrasion, making it suitable for applications where the tool or component is subjected to repeated friction or contact with abrasive materials.
Increased Strength: Hardened steel has higher tensile, compressive and yield strengths, allowing it to withstand higher loads and stresses without permanent deformation or failure.
Improved cutting performance: Hardened steel maintains a sharp edge for longer, allowing for more efficient cutting, machining and forming of materials.
Increased Tool Life: Hardened steel can significantly increase the life of tools and components, reducing the frequency of replacement and maintenance and lowering overall operating costs.
Improved Dimensional Stability: Hardened steel is less susceptible to distortion, warping or bending under mechanical loads or thermal cycling, ensuring greater dimensional accuracy and consistency in machined parts.
Increased surface hardness: Hardened steel surfaces are more resistant to scratching, denting and other forms of surface damage, resulting in improved durability and appearance.
Resistance to distortion: Hardened steel maintains its shape and integrity at high temperatures, making it suitable for applications involving elevated temperatures or thermal cycling.
Greater corrosion resistance: Some hardened steel grades exhibit improved corrosion resistance, reducing the risk of rusting, tarnishing or degradation when exposed to moisture, chemicals or harsh environments.
Common Hardening and Tempering Processes for Knife Steel
Hardening
The hardening process involves heating the metal to a specific temperature to dissolve its constituents into a solution. The metal is then solidified and strengthened to change any defects in its structure. As a result, the toughness of the metal or alloy is increased, making it less susceptible to bending.
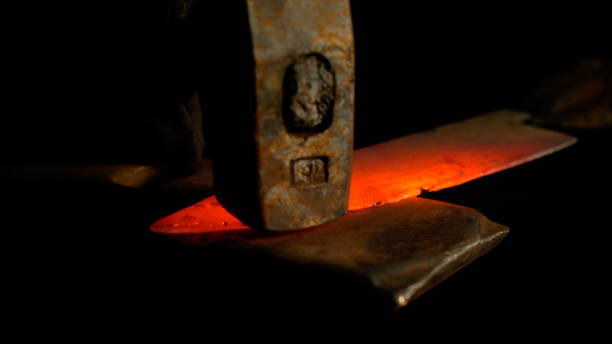
By heating the knife steel to 1050 to 1090°C (1922 to 1994°F) and then rapidly cooling it by quenching, the steel becomes harder but also more brittle.
To reduce the brittleness, the material is typically tempered by heating it to 175-350°C (347-662°F) for 2 hours. This process helps achieve a hardness of 53-63 HRC and provides a good balance of sharpness retention, grindability, and toughness.
Annealing
The annealing process has a significant effect on the malleability of the steel. Malleability refers to the ability of a material to be easily shaped or formed without breaking. By subjecting the steel to controlled heating followed by cooling, the annealing process increases its malleability. This makes the steel more manageable and easier to work with in subsequent manufacturing processes, such as forging or rolling.
In addition, the improved malleability resulting from annealing also reduces the likelihood of fractures or cracks in the steel. The internal stresses that can lead to these defects are effectively relieved during the annealing process, making the steel more resistant to failure under applied loads.
Tempering
Tempering can reduce the brittleness of steel and increase its strength. To reduce brittleness and maintain hardness, the steel is heated below the critical point during tempering.
It is important to temper immediately after quenching, ideally within one hour. Allowing the blade to cool to room temperature prior to tempering is critical to prevent any interruption in the transformation to martensite and potential impact on the quenching effect. The properties of the material vary depending on the tempering temperature: higher temperatures result in a softer and more ductile material, while lower temperatures result in a harder and more brittle material.
Temperatures below 175°C (347°F) should be reserved for special cases where extreme hardness is required, as very low tempering temperatures can make the material excessively brittle. Similarly, temperatures above 350°C (662°F) should be avoided to prevent embrittlement and reduced corrosion resistance. It is also important to avoid exposing the tempered blade to temperatures above the tempering temperature, such as during grinding, as this can affect the performance of the blade.
Surface Hardening
This is a process that makes a material harder on the outside than at the core. Since quenching makes the material brittle, surface hardening is used for materials that require toughness but still need to maintain a strong wear layer.
Normalizing
Like annealing, this process improves the toughness and flexibility of steel by heating it to a critical level and holding it there until a change occurs.
How to Heat Treat a Knife, Step by Step.
Step 1: Select the steel
Depending on the specific characteristics you are looking for, such as hardness, toughness, and corrosion resistance, consider selecting an appropriate steel for your knife. Some popular options to consider are high carbon steels such as 1095, tool steels such as O1 or D2, or stainless steels such as 440C or CPM-S30V.
Step 2: Prepare the blade
Begin by forming the steel into the preferred shape for the knife blade, either by machining or forging. Be sure to thoroughly clean the blade and remove any contaminants before proceeding with the heat treatment process.
Step 3: Austenitizing
To achieve the austenitizing temperature, use a heat source such as a propane forge, electric furnace or oxy-acetylene torch to heat the blade. The specific austenitizing temperature may vary depending on the type of steel, but typically ranges from 1400°F to 2100°F (760°C to 1150°C). Ensure that the heating process is even and gradual to avoid overheating or creating localized hot spots on the blade.
Step 4: Soak
Once the blade has reached the austenitizing temperature, it is held at that temperature for a period of time called the soak time. This allows the internal structure of the steel to fully convert to austenite and ensures uniform heating throughout the blade.
Step 5: Quench
After soaking, the blade is rapidly cooled by quenching in a quenching medium such as oil, water or air. The choice of quenching medium depends on the type of steel and the desired properties. Be careful when quenching to avoid warping, cracking or other forms of distortion.
Step 6: Tempering
After the blade is hardened, it is often tempered to reduce brittleness and improve toughness. The blade is heated to a lower temperature, typically between 350°F to 600°F (175°C to 315°C), and held at that temperature for a specified time. The exact tempering temperature and time will depend on the steel and the desired properties.
Step 7: Cooling and Finishing
After tempering, allow the blade to cool naturally to room temperature. Once cooled, the blade may require additional finishing processes such as grinding, polishing or sharpening to achieve the desired shape, surface finish and edge sharpness.
Step 8: Optional Processes
Depending on the steel and its intended use, additional processes such as cryogenic treatment, stress relieving or surface hardening may be applied to further enhance the blade’s properties or performance.
Step 9: Test
Finally, test the blade to ensure that it meets the desired specifications for hardness, toughness and other mechanical properties. Perform cutting tests, edge retention tests, or other evaluations to verify the performance of the blade prior to final assembly or use.
Conclusion
Heat treating knife steel is essential for creating blades that offer superior edge retention, wear resistance, strength, and durability. By enhancing these properties, hardened knives deliver consistent cutting performance and reliability, making them indispensable tools for a wide range of applications, from everyday tasks to specialized use cases in various industries. If you’re looking for quality multitools and knives at a competitive price, feel free to contact Volken.